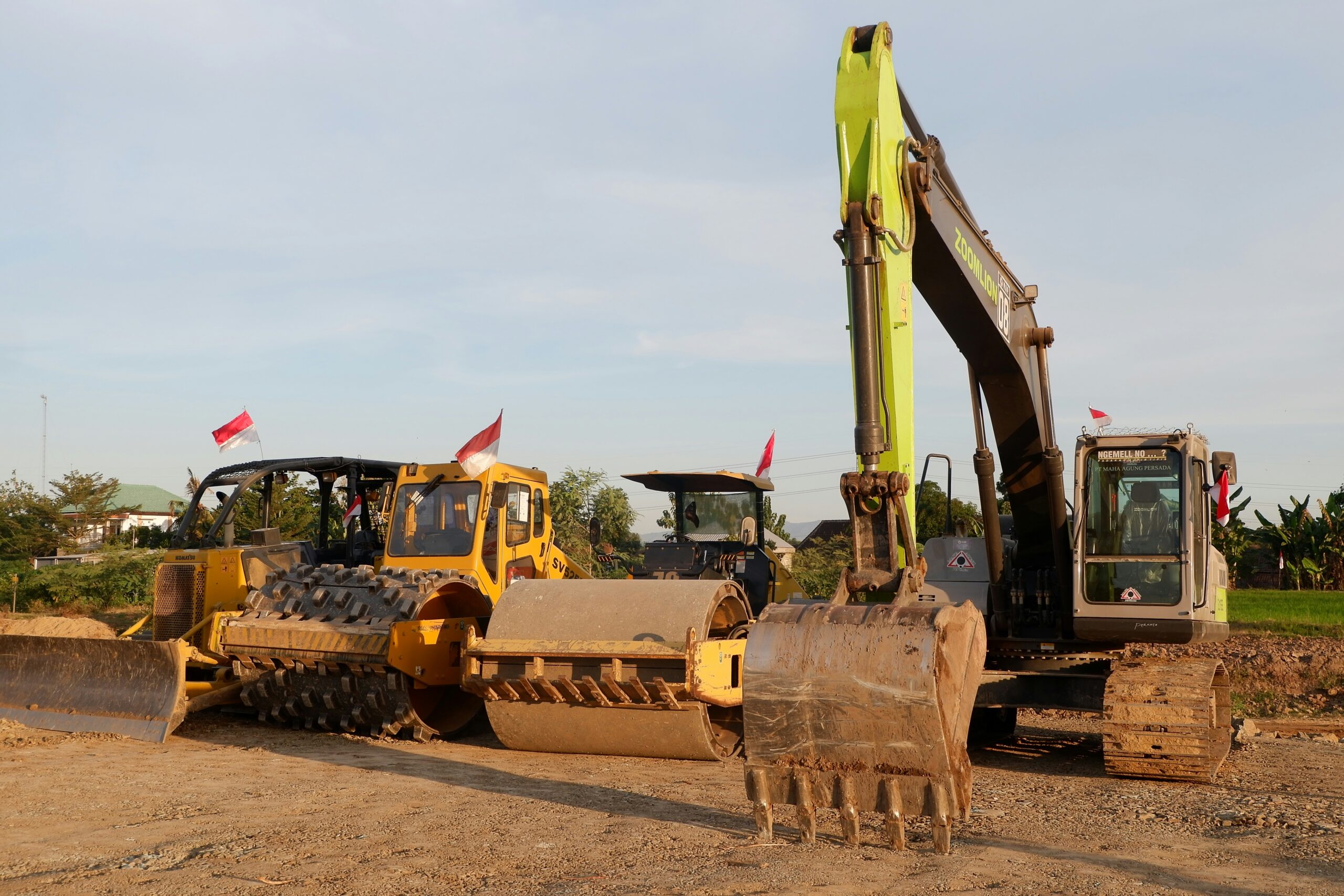
Efficiency and cost management are paramount in business operations in construction, agriculture, or any sector requiring heavy or specialized equipment. Acquiring new and pre-owned equipment is one effective strategy to optimize productivity without compromising quality. This article explores the advantages and considerations of integrating new and pre-owned machines into your operations, ensuring that you make the most informed decisions to enhance efficiency and drive success.
The Benefits of Investing in New Equipment
Investing in new equipment often has several inherent benefits that can justify the initial expenditure, especially for businesses looking to capitalize on the latest technological advancements.
Latest Technology and Innovations:
New equipment usually features the latest technology, which can significantly increase efficiency and productivity.
Modern machinery often includes better emissions controls and energy efficiency, which can reduce overall operational costs and improve compliance with regulatory standards.
Reliability and Warranty:
New equipment comes with manufacturer warranties, providing peace of mind and protection against initial defects or operational failures.
New machines’ reliability means less downtime due to repairs, which can critically affect project timelines and profitability.
Customization and Compatibility:
Purchasing new allows for customization options that match specific operational needs, ensuring that the equipment fits seamlessly into your existing workflow.
Newer equipment models are often easier to integrate with advanced technology systems, such as GPS tracking and automated systems, enhancing overall operational efficiency.
Capitalizing on Pre-Owned Equipment
While the allure of new equipment is strong, there are compelling reasons to consider pre-owned options as well.
Pre-owned equipment offers a practical and cost-effective solution for many businesses, especially startups or those looking to expand operations without substantial capital outlays.
Cost-Effectiveness:
Pre-owned equipment typically costs significantly less than new models, allowing for reduced financial strain and more flexible capital allocation.
Used equipment has lower depreciation rates, which means it retains more of its value over time, offering better cost-to-resale value ratios.
Immediate Availability:
Unlike new equipment, which may require ordering and manufacturing time, pre-owned machines are often available for immediate purchase and deployment.
This can be particularly advantageous for projects with tight deadlines or for unexpectedly replacing critical equipment that has failed.
Proven Performance:
Used equipment has a track record of performance, and existing reviews or product histories can help new owners anticipate potential issues and maintenance needs.
Operating a familiar model can reduce training time for staff, further enhancing operational efficiency.
Choosing Between New and Pre-Owned
Deciding whether to invest in new or pre-owned equipment should be guided by several strategic considerations:
Project Requirements:
Analyze the scope and duration of current and future projects. Pre-owned might be more economical for short-term needs or projects where the equipment will face heavy wear and tear.
Financial Health:
Assess your business’s financial state. If cash flow is a concern, pre-owned equipment may allow you to preserve capital for other business areas.
Risk Tolerance:
Consider the potential risk of downtime. New equipment might be more reliable, but consider whether your business can handle occasional interruptions from used items.
Maintenance Strategies to Maximize Equipment Lifespan
Whether you choose new or pre-owned equipment, proper maintenance is key to maximizing its lifespan and maintaining operational efficiency:
Regular Maintenance Checks:
Schedule regular inspections and adhere to maintenance guidelines specified by manufacturers for new equipment.
Conducting more frequent checks on pre-owned equipment may be wise, especially if the machine’s history is unknown.
Timely Repairs and Replacements:
Address repairs promptly to prevent minor issues from developing into major problems that can cause significant downtime.
Keep an inventory of essential spare parts for critical equipment to minimize downtime in case of sudden failures.
Training for Operators:
Ensure that all operators are fully trained on the specific models they will be using to prevent operator error, which can lead to breakdowns and increased wear and tear.
Consider refresher courses or new training sessions when acquiring different types of machinery or upgrading to newer models.
Choosing the right equipment, whether new or pre-owned, requires a strategic approach considering immediate needs and long-term operational goals. By understanding each option’s benefits and potential drawbacks, businesses can make decisions that enhance efficiency and align with financial strategies and growth objectives. Proper maintenance and skilled operation are crucial, regardless of the age of the equipment, to ensure that every machine performs at its best, contributing to the overall success and profitability of your operations.